The cover of Raconteur.net’s independent insert, as published in The Sunday Times edition of the UK newspaper, The Times showcases digital transformation in the manufacturing industry as an orchestra with a maestro at the helm – perform in concert, transform successfully. Choose to ignore these guiding directions and be exposed to a cacophony of cross-purposes noises, rather than a symphony.
The ‘Special Report,’ as it’s termed, explores not if the digitisation of manufacturing is ‘inevitable’ or not (a question already answered), but, rather, ‘how best to digitise, and what’s at stake if companies do not.’
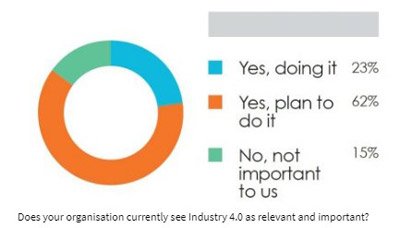
What is at stake if companies do not digitise? How does a manufacturing company digitise successfully and effectively?
In the United Kingdom, more than two-thirds (67%) of respondents in the Annual Manufacturing Report Survey have said that they’re ‘aware’ of Industry 4.0, as it’s better known.
Better yet, 23% are already moving over to digitisation and automation of their systems, while 62% are actively planning the move.
And regardless of where they are in the process, all respondents have mentioned making significant investments in automation in 2018-2019, with an understanding that all these major transformations require one very significant piece at the core:
A high level of factory connectivity ‘exploited to the full.’
But there’s room for improvement across Europe. Forty-six per cent of German companies, for example, report implementing Industry 4.0 technologies (and report feeling confident about their implementations).
When compared to the UK’s own 25% of manufacturers who report feeling they ‘have an adequate understanding of the threats and opportunities of Industry 4.0’, there’s clearly room for improvement and a need to see the specifics of how to implement these transformations.
What is Digital Transformation in the Context of Industry 4.0?
Known as the ‘fourth’ industrial revolution, Industry 4.0 is a complete overhaul of manufacturing companies, top to bottom and, necessarily, both internal and organisational structure and external, client-facing operations.
It’s a disruption to the way things are being done, to be sure, but one that is inevitable. Nor does ‘disruption’ necessarily need to mean disaster.
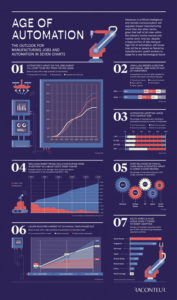
Done right, the digital transformation processes and technologies at the heart of this newest industrial revolution can place entire countries at the leading edge of innovation – and, by extension, profitability.
But given that ‘25% of manufacturers…report feeling they have an adequate understanding of the threats and opportunities of Industry 4.0’, it’s worth it to understand what we’re talking about when talking about this next wave.
Industry 4.0 is a collection of changes and innovations occurring in industries that previously relied on a certain level of machine-operation and human interfacing. Industry 4.0 obviously affects manufacturing, but this is not the only sector that is poised for transformation that is digitally-driven. Sectors as diverse as healthcare to public transportation, education, hospitality, tourism, research and academia – all are fair game for these transformative practices.
And what do these practices look like? Well, they’re all about things like automation, convergence, connectivity, deep learning, virtual and augmented reality, predictive analytics, and more.
As you can see, even one sphere – that of automation – is intricately connected with other changes such as AI, remote communication, reliance on robotics, and more. On the human side, this will require an up-skilling of the workforce (rather than a reduction).
Drill down even further, from concepts to the actual technologies executing on these concepts, and you’ll find devices, digital tech, networks, robotics, AI, and advanced analytics at the heart of these transformations.
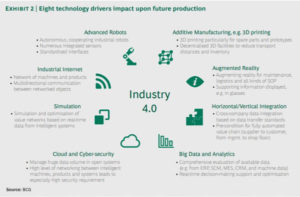
Now, when it comes to manufacturing and production-heavy industries, here’s what these tech drivers look like, specifically:
‘Industry 4.0 technologies – such as automation, robotics, software, sensors, virtual reality, 3D printing, big data, human-machine interface to name but a few – are already shaping the agenda of UK manufacturing across every sector.’ – Annual Manufacturing Report
The jury’s still out on whether the UK is or is not actually ‘ready’ for this next digital industrial revolution – one that many of us as consumers, on a microcosmic level, are already living in.
Think IoT smart home networks and digital assistants, predictive digital signage and voice-enabled search.
If the saying by Picasso goes, ‘Every act of creation is an act of destruction,’ the question also becomes, can we create without destroying? Instead, can we deconstruct to rebuild something better?
If it’s inevitable, what can UK companies really stand to gain from embracing these new enhancements as early adopters, rather than late-to-the-party?
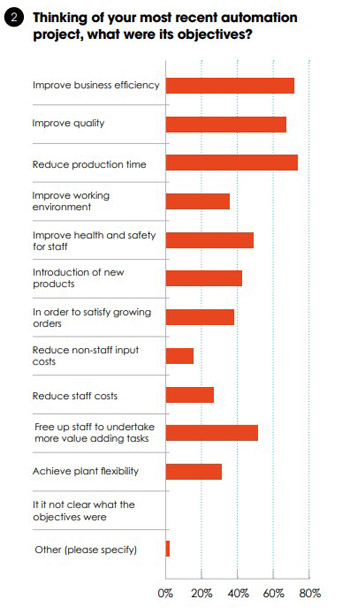
Why and how UK Companies can extract benefits from Embracing Digital Transformation
The biggest fear of manufacturing companies – which, in turn, drives deep resistance to this incumbent change – is that automation will make humans obsolete.
But, the reality is that automation is already freeing individuals up to diversify the company’s products and services, offering corollary options like lease/hire/rental of product. In fact, only 27% of industrial automation leads to a reduction in staff costs.
Now, there are many advantages to be gained from automation, including:
- Improving business efficiency
- Improving quality
- Reduce production hire
- Improvement working environment
- Introduction of new plants
- Freeing up staff to undertake more value-adding tasks
- Achieving plant flexibility
Meanwhile, the outlook and expectations for connectivity within a manufacturing and production setting are equally as bright:
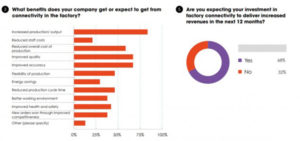
5 Common Principles of Successful Industry 4.0 Implementation
It’s easy to think about and focus on the pitfalls of digital transformation during the Industry 4.0 epoch.
But what would be the point in that? Instead, let’s say that the UK has a major opportunity that it can capitalise on.
Its competitive advantage lies in the fact that its Internet economy accounts for a higher proportion of its GDP than any other member of the G20. Just looking at this graph, we can see that there are clear actions – such as developing a clear business case – companies can take to move toward implementation.
Rapidfire growth in the Internet sector of the economy spells a greater number of employment opportunities, continual investments in network-based infrastructure (such as the 5G network rollout by 2020), training, and education required for full-scale Industry 4.0 adoption.
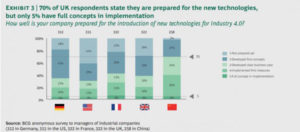
Even so, progress in the UK has, so far, moved along the pace of a viscous liquid:
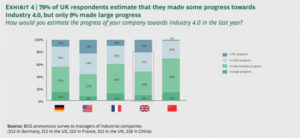
Will companies have it rough? Yes, undoubtedly. Change is no easy thing. And anyone on a chemical or manufacturing plant floor can tell you just how vast a difference a simple thing like a functioning sensor can make on the rest of the plant’s operations.
Everything is interrelated. But that’s where these implementation principles, when followed, will guide companies to successful digital transformation. The point is to plan for and expect this interconnection and then operate alongside it.
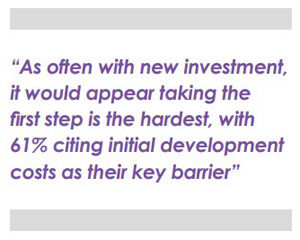
1) Building An Integrated Operations Ecosystem
Successful implementation of these digital technologies and their supporting principles relies on an integrated operations ecosystem.
When PWC UK took a look at connectivity and automation in current UK companies, they found that it’s a ‘must-have for companies looking to harvest the full potential of digital, enabling them to improve cost and leverage data analytics.’
Instead, a large majority of companies in the UK are currently ‘only selectively’ exploiting this relationship in their facilities:
So what does an end-to-end digitisation and data integration of the value chain actually call for?
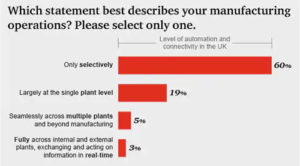
Implementing an integrated operations ecosystem requires management to essentially master collaboration and put in place a clear strategy for:
- Offering digital products and services
- Operating connected physical and virtual assets
- Transforming and integrating all operations and internal activities
- Building strategic partnerships
- Optimising customer-facing activities using these new technologies (often predictive in nature)
2) Rethinking KPIs and how ‘success’ is Measured
If the platforms are new, and the behaviours are fresh, this means that measurement of ROI and metrics of success need to run alongside this change.
It’s no coincidence, then, that the era of Industry 4.0 is coming up with a new kind of focus on metrics: Growth and the North Star.
A company’s North Star is a pre-determined desirable outcome against which all future activities will be weighed. The only thing that matters is that this North Star is achieved – because it best reflects the company’s priorities.
And, of course, these KPIs should always be geared toward an uptick, growth – be that measured through customer acquisition, investments, market share, revenue, etc.
A great example of this is seeing a shift in previous labour-intensive processes that are manual with automated practices that significantly speed up the time in production.
3) Moving to Servitisation
A third common principle for successful implementation is directly related to what we saw with the integrated operations ecosystem.
Servitisation is an inevitable consequence of that transformation. It’s all about manufacturers beginning to see themselves beyond the role of just producers of tangible products.
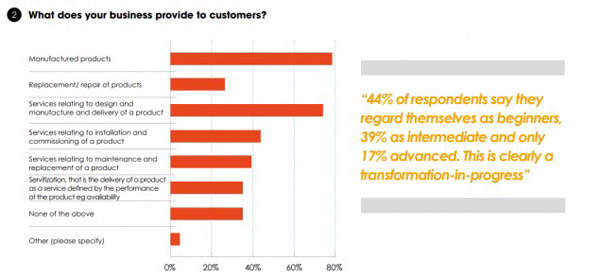
The ‘achievement of plant flexibility’ we saw previously as an advantage mimics this. In fact, the somewhat unintended effects of servitisation were that:
- 31% of companies found it reduced the overall cost of production
- 22% said it increased the flexibility of production
Servitisation calls on manufacturers to transform ‘themselves from sellers of products to deliverers of services’ because ‘companies [are striving for] new ways to please customers – and hang onto them.’
The power of providing a combination of products and services means that companies can diversify their revenue streams, introducing a greater number of ways to serve their clients’ or customers’ various needs under one brand.
Perhaps the best example of this was Microsoft. Under the leadership of Satya Nadella, the introduction of cloud-based services such as One Drive diversified Microsoft’s offerings in 2014 and 2015, at a time when all other flagship products were losing to Apple.
The result was that these servitised offerings gave Microsoft one of its most profitable quarters.
4) Rely On Proven IT Security Processes
Digital transformation is innovative, profitable, and advantageous on many fronts.
But it’s not without its vulnerabilities. Some see the increasing reliance on digital as a gateway to a commensurate rise in cyber-attacks.
While it’s true that these attacks are common, there are also a host of precautions companies can take. These proven security implementations must occur alongside these digital transformations.
While some are preventative in nature, equipping manufacturers from the outset, others are designed to be triggered when direct attacks are waged. The point is to extend these IT security processes to production floors, protecting actual plant equipment or practices. This can include strategies like network segmentation and firewalls.
There are also instruments which allow centralised and streamlined command of all connected IoT devices that update simultaneously. As we feel less like beginners and embrace digital transformation, the sophistication of these security techniques is rising in kind.
5) Create a Tangible Timeline for Transformation
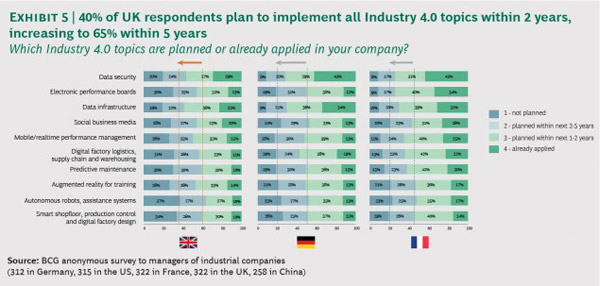
There are just so many prongs to digital transformation. For this opportunity to be seized by UK manufacturers headed into Industry 4.0, it must be seized correctly, from the outset.
Addressing data infrastructure, putting in place digital factory logistics – these are things that cannot be handled in a piecemeal way. That’s why it’s so important to plan these changes at the same time, addressing what it would mean for internal and external operations.
What are the minuscule human- and machine-related changes that will have to occur?
What are the shifts in business culture that have to organically develop over time?
The hardest thing to remember at the beginning of any transformation – let alone one as fundamental as Industry 4.0 – is that this is a long-term industrial strategy. You’re in it until the next natural, inevitable evolution.
Whatever that looks like.
For now, UK companies have to bridge the gap between potential and move to practical. Even starting to address the previous four spheres with a concrete timeline will be one giant step for manufacturing-kind.
Conclusion
There’s one very glaring contextual detail that we can’t leave out. It’s akin to Harry Potter’s ‘He Who Must Not Be Named’. No one wants to say it. But everyone’s thinking it. Brexit.
When surveying manufacturing companies in the UK involved with some level of Industry 4.0 initiatives, KPMG found that the perception of Brexit as inherently unstable was causing companies to consider several ‘radical measures’ to plan for this change.
And many of these measures are about integrating operations, not only across EU regions but through technological enhancements.
Martin Thomas, European Marketing Manager at Radwell International Ltd explains more, “This allows for greater connectivity across industries – what is coming to be known as ‘coordinated mobility ecosystems’ of car manufacturers, fleet managers, telecommunications, infrastructure, finance, insurance and cyber security. Change is absolute and already underway. We’ve voted for it. Now it’s time to get behind it.”
T 01782 482613
www.radwell.co.uk